15 Years Factory wholesale melamine chip and dip plate to Washington Importers
15 Years Factory wholesale melamine chip and dip plate to Washington Importers Detail:
Specification | |
Item Name | 13inch Round Melamine Chip and Dip Plate |
Item No. | PT070 |
Shape | Round |
Body Color | White |
Decal Color | 4 colors print |
Finish | Glossy |
Style | Fashion |
Motif Design | Customized |
Shape Design | OEM/ODM |
Test Standard | FDA,PROP 65,EN71,LFGB etc. by SGS or ITS |
Packaging | 6pcs/box,24pcs/carton |
Dimensions | |
Length | 33 cm |
Width | 33 cm |
Height | 2.4 cm |
Capacity | N/A |
Material | |
Body Material | 100%melamine |
Decal Material (if need) | 4 colors print (CMYK), or spot color printing, RoHS certificate |
Imprint (if need) | Seiko ink type 1000 or other type, RoHS certificate |
Accessories Information | |
Lid included | No |
Other | No |
Weights | |
Net Weight (kg) | 6.5 |
Shipping Weight (kg) | 7.7 |
Product detail pictures:
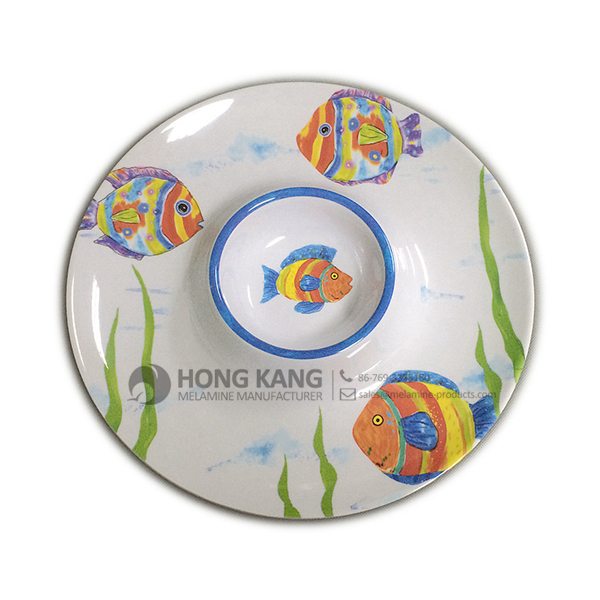
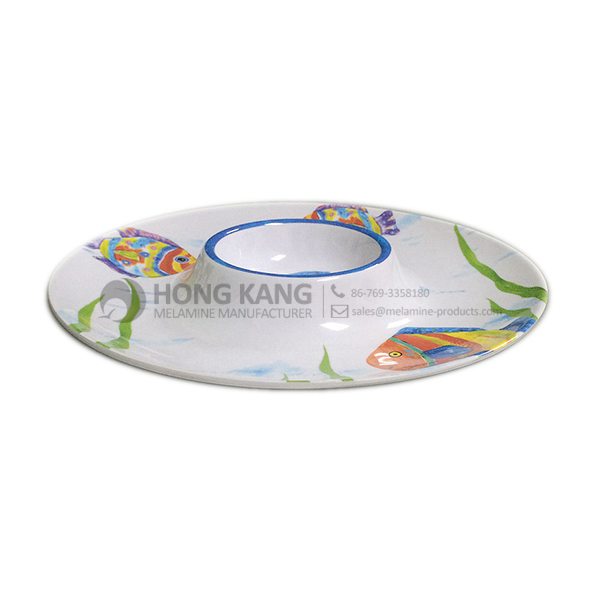
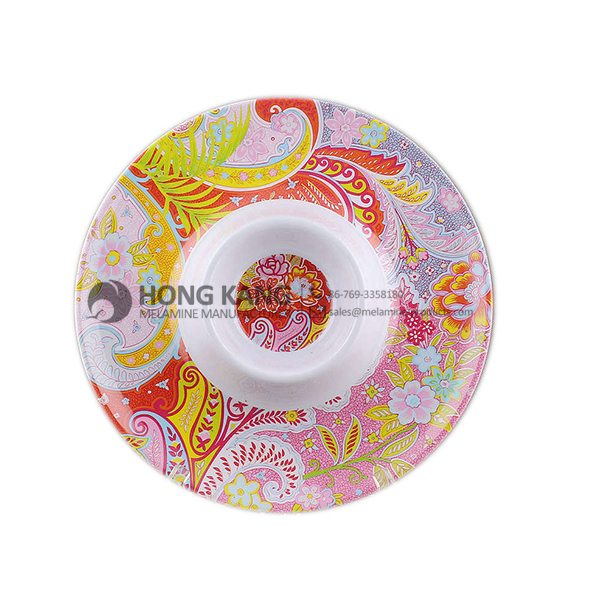
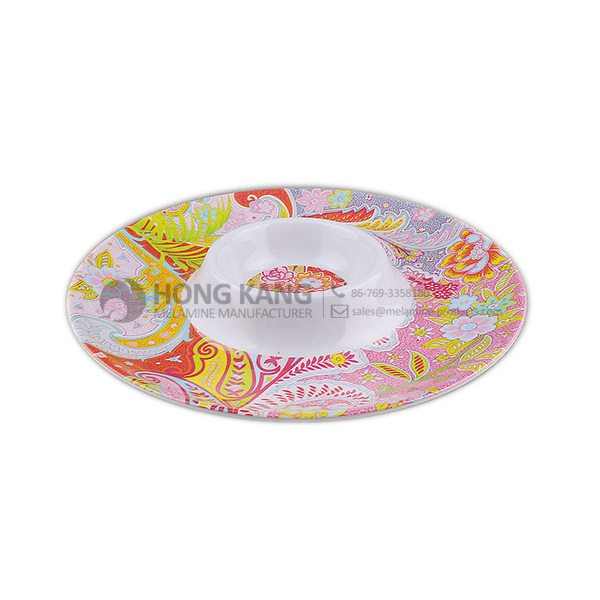
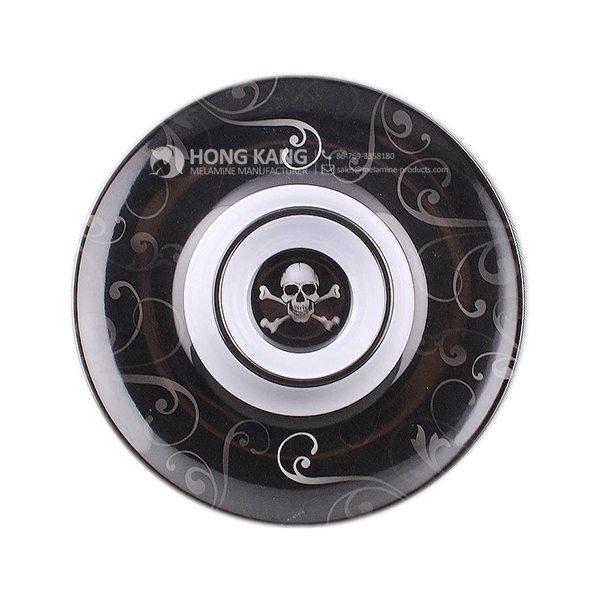
Related Product Guide:
Affordable Types of Dinnerware Sets
Choosing The Best Dog Bowl and Feeder for Your Dog
owing to excellent assistance, a variety of top of the range items, aggressive costs and efficient delivery, we take pleasure in a very good standing amongst our shoppers. We've been an energetic corporation with wide market for 15 Years Factory wholesale melamine chip and dip plate to Washington Importers, The product will supply to all over the world, such as: Argentina , Lithuania , Iran , Although continuous opportunity, we have now now developed serious a friendly relationship with many oversea merchants, such as ones through Virginia. We securely assume that the merchandise regarding t shirt printer machine is often good through a great number of having its good quality and also cost.
FAQ: 1.Q: Where is your factory located? How can I visit there? A: Our factory is located in Guangdong province, China. Warmly welcome to visit us! 2.Q: What is the material of your products? A: The material is melamine. 3.Q: How can I get some samples? A: We can send the samples by Express/DHL/FedEx/UPS etc. 4.Q: How does your company do regarding quality control? A: We have a very strict QC system. Our inspectors have been closely monitoring the production process from the selection of raw materials to the final step of the finished products. 5.Q: Can you print our logo on the product & packing? A: Yes, We can print your logo on our products.
* Do Not Touch On Fire Directly | |
---|---|
* Do Not Washing By Steelwire Ball | |
* Non-Microwave Ovens | |
* Dishwasher Safe |
Now chatting: http://www.leawaysschool.com/solution.html
Contact Us: http://www.leawaysschool.com
Wholesale Collapsible Silicone Bowl – Made-in-China.com 597 products China Wholesale Collapsible Silicone Bowl – Select 2016 high quality Wholesale Collapsible Silicone Bowl products Audited Suppliers Wholesale Portable Food-Grade Eco-Friendly Collapsible Silicone Foldable Bowl for Dog . Guangdong, China; ISO 20000, OHSAS/ OHSMS 18001, HSE, GMP, BSCI. Food Bowl & Water Bowl – China Pet Bowl, Pet Bowl Manufacturers 2761 products Audited Suppliers Audited Supplier Use high-quality felt, eco-friendly and nice hand . . Collapsible Pet Food Bowl Foldable Dog Water Bowal. Silicone Rubber Bowl – Alibaba Eco-friendly Food Grade Folding Colorful Pet Bowl For Travel silicone rubber dog bowl . Sedex Audit factory FDA standard collapsible silicone rubber bowl. Compartment Bowl, Compartment Bowl Suppliers and Silicone Collapsible Bowl with Cover Microwave 3 compartment dinner box BSCI audit colorful LFGB passed plastic food compartment bowls . wholesale plastic mini dessert plates take away salad bowl eco-friendly round plastic food Microwave Safe Bowl – Alibaba Eco-friendly microwave safe fine white LM552 porcelain soup bowl for wholesales · Chaozhou . Microwave safe silicone rubber collapsible folding soup bowl with FDA standard BSCI audit wing shape microwave safe double injection bowl. Heat Resistant Bowl – Alibaba Top quality heat resistant light green melamine square deep plate bowl · Xiamen Bestwares . BSCI audit Heat Resistant round shape plastic salad bowl. Plastic Bowl, Plastic Bowl Suppliers and Manufacturers at Alibaba.com 5qt plastic collapsible bowl Huangyan · Taizhou Huangyan Gelin Christmas hot sale eco friendly plastic salad bowl disposable with lid · Shantou Europe-Pack Connect with 6,921 Pet Bowl Manufacturers – Global Sources Collapsible Pet Bowl for Easy Carrying and Storage Min. Pet Products Removable Eco-friendly Silicone Pet Bowls Min. Location: China (mainland) Small Orders: Accepted Staff: 150 to 199 Certs: BSCI,SGS .. verified Business Registration, as licensed by relevant government; This supplier has a supplier audit from Connect with 6,452 Collapsible Cup Manufacturers – Global Sources Find 6452 Collapsible Cup manufacturers from Global Sources 鈽?Source top Eco-friendly Collapsible Water Bottle Min. . a supplier audit from an independent 3rd party; This supplier has exhibited at one . Middle-sized Collapsible Bowl with Protective Lid, Made of Food-grade PP and TPR Material · Compare Product. China BPA Free Travel Bowl Folding Silicone Dog Bowls China BPA Free Travel Bowl Folding Silicone Dog Bowls with High-Quality 1Silicone Collapsible Pet Travel Bowl, dog food/water bowl – the ideal BSCI Factory Audit Approved. Wholesale Eco-friendly Good Cook Silicone Spatula. Wholesale Collapsible Silicone Bowl – Made-in-China.com 597 products China Wholesale Collapsible Silicone Bowl – Select 2016 high quality Wholesale Collapsible Silicone Bowl products Audited Suppliers Wholesale Portable Food-Grade Eco-Friendly Collapsible Silicone Foldable Bowl for Dog . Guangdong, China; ISO 20000, OHSAS/ OHSMS 18001, HSE, GMP, BSCI. Food Bowl & Water Bowl – China Pet Bowl, Pet Bowl Manufacturers 2761 products Audited Suppliers Audited Supplier Use high-quality felt, eco-friendly and nice hand . . Collapsible Pet Food Bowl Foldable Dog Water Bowal. Silicone Rubber Bowl – Alibaba Eco-friendly Food Grade Folding Colorful Pet Bowl For Travel silicone rubber dog bowl . Sedex Audit factory FDA standard collapsible silicone rubber bowl. Compartment Bowl, Compartment Bowl Suppliers and Silicone Collapsible Bowl with Cover Microwave 3 compartment dinner box BSCI audit colorful LFGB passed plastic food compartment bowls . wholesale plastic mini dessert plates take away salad bowl eco-friendly round plastic food Microwave Safe Bowl – Alibaba Eco-friendly microwave safe fine white LM552 porcelain soup bowl for wholesales · Chaozhou . Microwave safe silicone rubber collapsible folding soup bowl with FDA standard BSCI audit wing shape microwave safe double injection bowl. Heat Resistant Bowl – Alibaba Top quality heat resistant light green melamine square deep plate bowl · Xiamen Bestwares . BSCI audit Heat Resistant round shape plastic salad bowl. Plastic Bowl, Plastic Bowl Suppliers and Manufacturers at Alibaba.co

The after-sale warranty service is timely and thoughtful, encounter problems can be resolved very quickly, we feel reliable and secure.
