Wholesale Distributors for melamine cutting board for Ethiopia Manufacturer
Wholesale Distributors for melamine cutting board for Ethiopia Manufacturer Detail:
Specification | |
Item Name | 9.25inch Melamine Cutting Board |
Item No. | PT133 |
Shape | Rectangle |
Body Color | White |
Decal Color | 4 colors print |
Finish | Glossy |
Style | Fashion |
Motif Design | Customized |
Shape Design | OEM/ODM |
Test Standard | FDA,PROP 65,EN71,LFGB etc. by SGS or ITS |
Packaging | 12pcs/box,48pcs/carton |
Dimensions | |
Length | 23.3 cm |
Width | 14.3 cm |
Height | 0.3 cm |
Capacity | N/A |
Material | |
Body Material | 100%melamine |
Decal Material (if need) | 4 colors print (CMYK), or spot color printing, RoHS certificate |
Imprint (if need) | Seiko ink type 1000 or other type, RoHS certificate |
Accessories Information | |
Lid included | No |
Other | No |
Weights | |
Net Weight (kg) | 7.2 |
Shipping Weight (kg) | 8.5 |
Product detail pictures:
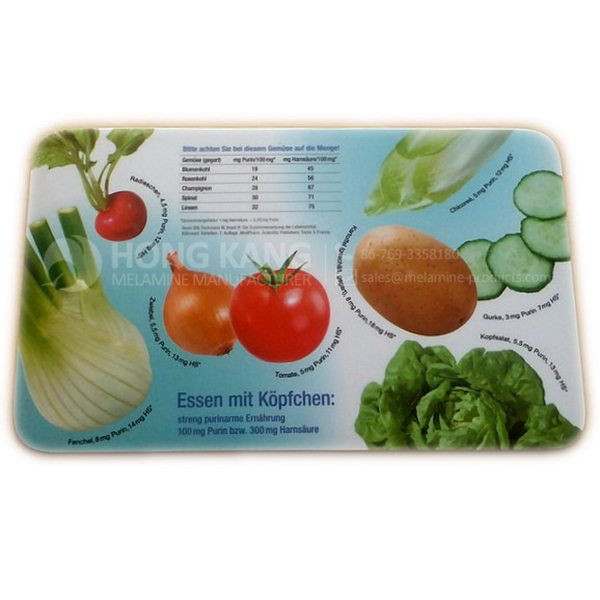
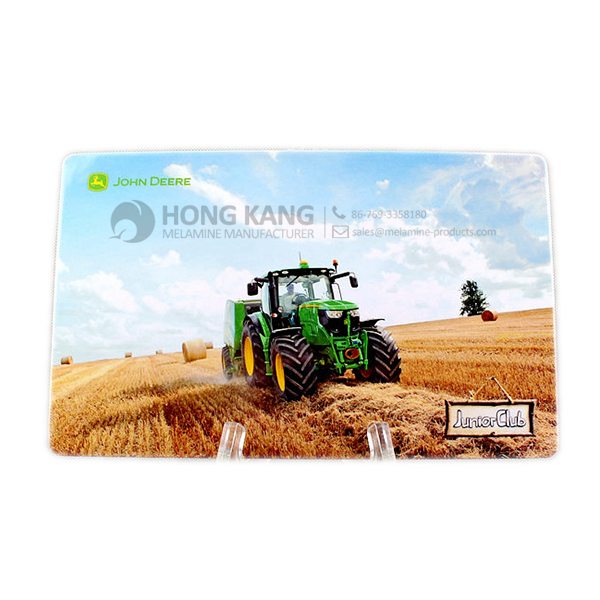
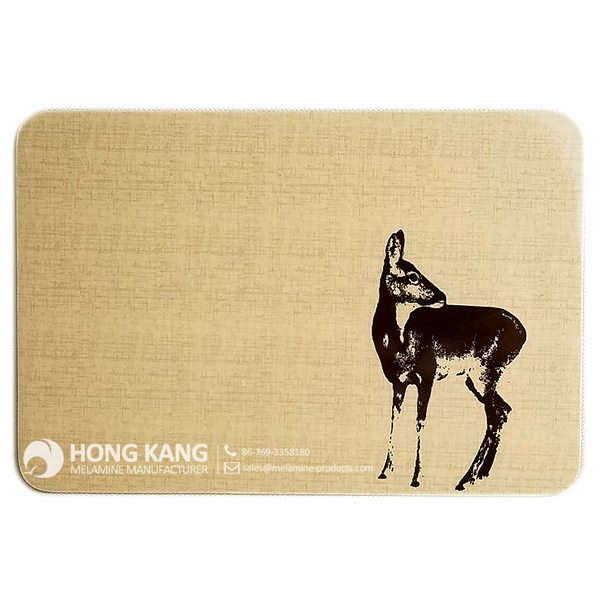
Related Product Guide:
Top Ten Power Toothbrushes
Affordable Types of Dinnerware Sets
Our advancement depends over the superior machines, exceptional talents and continually strengthened technology forces for Wholesale Distributors for melamine cutting board for Ethiopia Manufacturer, The product will supply to all over the world, such as: Wellington , Algeria , Curacao , Each year, many of our customers would visit our company and achieve great business advancements working with us. We sincerely welcome you to visit us at any time and together we will prevail to a greater success in the hair industry.
FAQ: 1.Q: Where is your factory located? How can I visit there? A: Our factory is located in Guangdong province, China. Warmly welcome to visit us! 2.Q: What is the material of your products? A: The material is melamine. 3.Q: How can I get some samples? A: We can send the samples by Express/DHL/FedEx/UPS etc. 4.Q: How does your company do regarding quality control? A: We have a very strict QC system. Our inspectors have been closely monitoring the production process from the selection of raw materials to the final step of the finished products. 5.Q: Can you print our logo on the product & packing? A: Yes, We can print your logo on our products.
* Do Not Touch On Fire Directly | |
---|---|
* Do Not Washing By Steelwire Ball | |
* Non-Microwave Ovens | |
* Dishwasher Safe |

The company has a good reputation in this industry, and finally it tured out that choose them is a good choice.
